В Industry 4.0 произошли значительные изменения: в то время как датчики в решениях по автоматизации в основном записывают переменные процесса и передают их в ПЛК в режиме реального времени, в Industry 4.0 доступны новые функции, такие как изменение рецепта, изменение формата или прогнозное обслуживание. Данные датчика, требуемые для этого, обычно не требуются для реальных задач автоматизации и обновляются реже - однако, они более обширны. Поскольку они часто объединяются централизованно с данными из других источников, например в облаке, они должны быть доступны по всему миру и в стандартизированном формате.
Принцип для каждой передачи данных
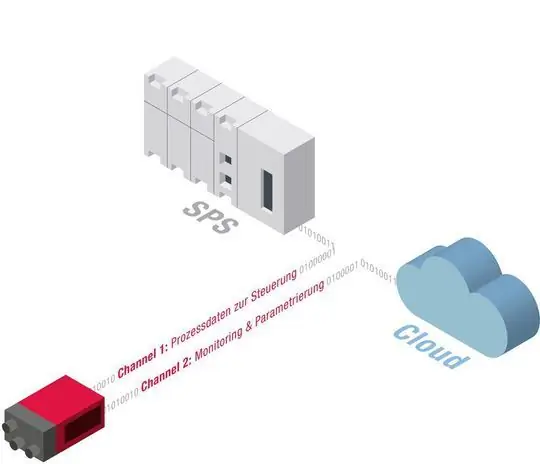
Как датчики тока подготовлены к этим требованиям? Каждый тип датчика предоставляет различные объемы данных, интерфейсы адаптированы к соответствующей сложности передачи данных: простые двоичные переключающие датчики передают значения процесса, сообщения о состоянии и диагностические сообщения через IO-Link. Более сложные датчики с более высокой функциональностью часто интегрируются в сети полевых шин реального времени. Они предоставляют значения процессов и аварийных сигналов, а также статусные и диагностические сообщения и могут быть полностью параметризованы с помощью системы управления. Это краткое резюме показывает: датчики тока не соответствуют специальным требованиям приложений Industry 4.0 для передачи данных.
Компания Leuze Electronic решает эту проблему с помощью нового изобретения: благодаря так называемому двухканальному принципу данные могут быть впервые разделены и предоставлены в соответствии с требованиями заказчика. В то время как данные для управления процессом передаются в режиме реального времени через первый канал датчика, информация для мониторинга и анализа машины проходит через второй.
Один датчик, два канала
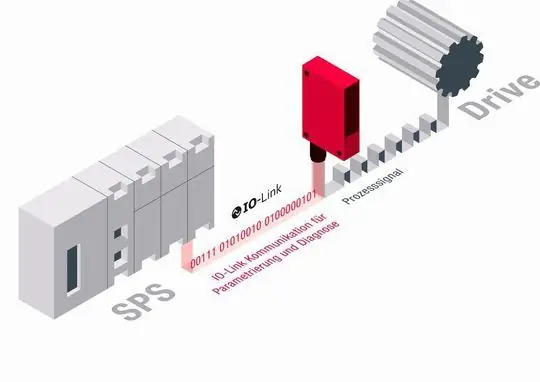
Как работает двойной канал на практике? Для бинарного переключающего датчика с подключением к ПЛК, что-то вроде этого: Если, например, сканер контрастности KRT18B используется в быстродействующей упаковочной машине для определения точной позиции метки реза, качество упаковки машины зависит от возможности переключения выхода в реальном времени. Поэтому переключающий выход контрастной кнопки лучше подключать непосредственно к приводу. Для включения мониторинга и анализа машины кнопка также имеет интерфейс IO-Link. Можно наблюдать технологические значения, функциональные резервы и параметризацию - или изменения рецепта и форматирования. С классическим интерфейсом IO-Link в режиме SIO (стандартный режим IO),это либо разрешает сигнал переключения, либо, по запросу, связь точка-точка с датчиком будет невозможна - только двухканальный принцип позволяет описанное приложение.
Тот же компьютер с функциями Industry 4.0: если данные должны быть доступны другим участникам автоматизации в облаке, например, для мониторинга и параметризации, вместо подключения IO-Link к ПЛК, подключение к IO-Link Требуется модуль связи с интерфейсом Ethernet и протоколом связи OPC-UA. Например, подключение к облаку осуществляется через пограничный шлюз IoT.
Дополнительная информация по трем вопросам к Инго Баумгардту
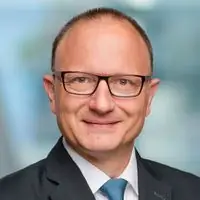
Инго Баумгардт - руководитель отдела сенсорной связи в Leuze electronic GmbH + Co. KG
Когда стоит использовать двухканальные датчики?
Двухканальный (= второй канал) был специально разработан для того, чтобы пользователи могли обмениваться динамическими, некритическими по времени данными с устройствами в дополнение к необходимым быстрым значениям процесса. Последние в основном представляют собой данные диагностики и мониторинга, которые предоставляют информацию о состоянии устройства и, следовательно, косвенно о доступности и производительности машины. Из-за незапланированных простоев или простоев машин быстро добавляются небольшие дополнительные усилия со стороны устройства.
Действительно ли датчики имеют два отдельных интерфейса - по одному для каждого канала?
Нет, двухканальный принцип не требует дополнительного физического интерфейса. Дополнительная информация передается по существующему кабелю как при использовании IO-Link, так и с OPC UA, что позволяет сохранить компактную конструкцию современных датчиков.
Насколько велики усилия, если я хочу использовать двухканальные датчики в новой машине или если я хочу модернизировать существующую машину с ней?
Здесь два понятия несколько отличаются. Чтобы сегодня управлять бинарным переключающим датчиком в двухканальном режиме, управление машиной должно быть расширено за счет связи с IO-Link. Для этого обычно используются мастер-модули, которые можно интегрировать в существующие системы ввода-вывода. Для машин, которые уже используют Profinet в качестве интерфейса процесса, расширение с помощью двухканального OPC UA ограничено обновлением используемого датчика, поскольку данные могут передаваться через существующую сеть.
Даже сложные датчики поддерживаются
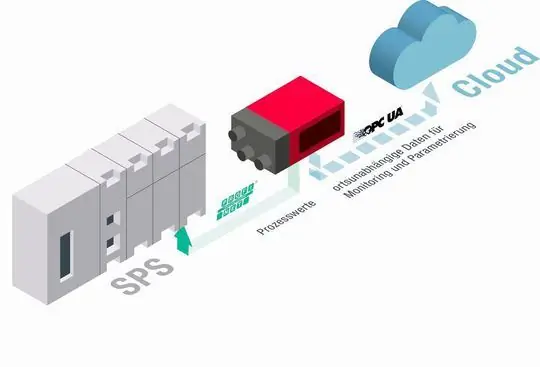
Leuze Electronic также предлагает двухканальное решение для сложных датчиков со встроенным интерфейсом полевой шины. Например, сканер штрих-кода BCL 348i предлагает интерфейс полевой шины Profinet, через который из контроллера выполняются параметры процесса и аварийные сигналы, сообщения о состоянии и диагностике, а также параметризация устройства. Для облачных приложений датчик представляет данные через интерфейс Industrial Ethernet, используя протокол связи OPC UA. (JV)