Композитные материалы, такие как углеродные или стекловолоконные композиты, являются особенно жесткими и прочными и используются для легкого строительства в самолетостроении, спорте, недвижимости, ветрогенераторах и автомобилестроении. Совместно с Röttger GmbH, Институт общего машиностроения факультета компьютерных наук и инжиниринга в TH Cologne Campus Gummersbach разработал систему из двух инструментов, которая оптимизирует процесс пропитки углеродных и стеклянных волокон. Это экономит производственные затраты и ресурсы при изготовлении волокнистых композитных компонентов.
Стеклянные и углеродные волокна производятся в пачках до 48 000 нитей, так называемых ровингов. С помощью процесса намотки ровинги могут быть обработаны в симметрично вращающиеся компоненты, такие как резервуары высокого давления или приводные валы. Для сохранения таких свойств, как определенная прочность, пучки волокон пропитывают эпоксидной смолой. В процессе намотки пропитка валиком смесью пластмассовых смол является наиболее распространенным методом. Ровинги направляются через вращающийся пропиточный валик, который транспортирует смолу из ванны в ровинг. Используемые в настоящее время инструменты для пропитки ограничены скоростью обработки около 1 м / с.
Более высокие производственные скорости от 1,6 м / с до 2 м / с
Система инструментов, недавно разработанная в TH Cologne в сотрудничестве с Röttger GmbH, теперь обеспечивает более высокую скорость производства. «С нашей новой системой инструментов мы создаем от 1,6 м / с до 2 м / с», - говорит руководитель проекта проф. Д-р. Патрик Тичельманн. «Это может сэкономить от восьми до десяти часов системного времени для очень больших компонентов».
Система состоит из двух компонентов: инструмента для пропитки и ультразвукового распределителя волокон. Инструмент для пропитки состоит из верхней и нижней оболочки, через которую волокна направляются и равномерно пропитываются эпоксидной смолой снизу и сверху. Из-за синусоидальной структуры верхней и нижней оболочки двенадцать ровингов могут обрабатываться параллельно.
СОВЕТ ПО СЕМИНАРУ Семинар «Легкие материалы в строительстве» знакомит с методами, принципами проектирования и методами строительства легких конструкций. Участники получают обзор различных легких материалов, изучают критерии выбора материалов и узнают о преимуществах, недостатках и рисках различных материалов.
Следующая информация
«Время процесса намотки уменьшается, производительность системы намотки значительно увеличивается в зависимости от продукта, а почасовая производительность машины также уменьшается. Более простое обращение и более короткое время очистки макс. От 10 до 20 минут вместо нескольких часов, как прежде, завершают работу системы », - объясняет профессор Тичельманн.
Легкий сборник
Собирайте идеи для облегченного строительства
Распространение волокна предшествует процессу. Недавно разработанный ультразвуковой распределитель волокон гарантирует, что волокна ранее были как можно более плоскими. Разбрасыватель имеет разбрасыватели с ультразвуковым возбуждением, которые вибрируют перпендикулярно зерну и, как и на вибрирующем столе, обеспечивают ровное распределение ровницы. «Эта комбинация распределителя волокна и инструмента гарантирует, что скорость пропитки намного выше, чем у используемых в настоящее время систем», - говорит профессор Тичельманн.
Экологичность: пропитка материалов в инструменте снижена более чем на 80%
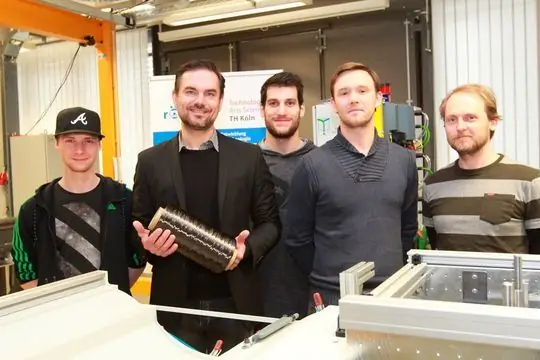
Другим преимуществом нового процесса по сравнению с обычными системами является более низкое потребление пластика. «Нам удалось сократить использование пропиточных материалов в инструменте более чем на 80 процентов. Это также уменьшает количество материалов, которые необходимо утилизировать », - говорит профессор Тичельманн.
Система намотки должна использоваться в качестве инструмента для всех будущих проектов в TH в Кельне, где требуются намоточные конструкции. Исследовательский проект «Процесс обмотки» проводился на факультете компьютерных наук и инженерии и в Институте общего машиностроения под руководством профессора, доктора технических наук. Патрик Тичельманн и находится в Röttger GmbH. Он был профинансирован Федеральным министерством экономики и энергетики на сумму 190 000 евро в рамках Центральной инновационной программы для МСП (ZIM).